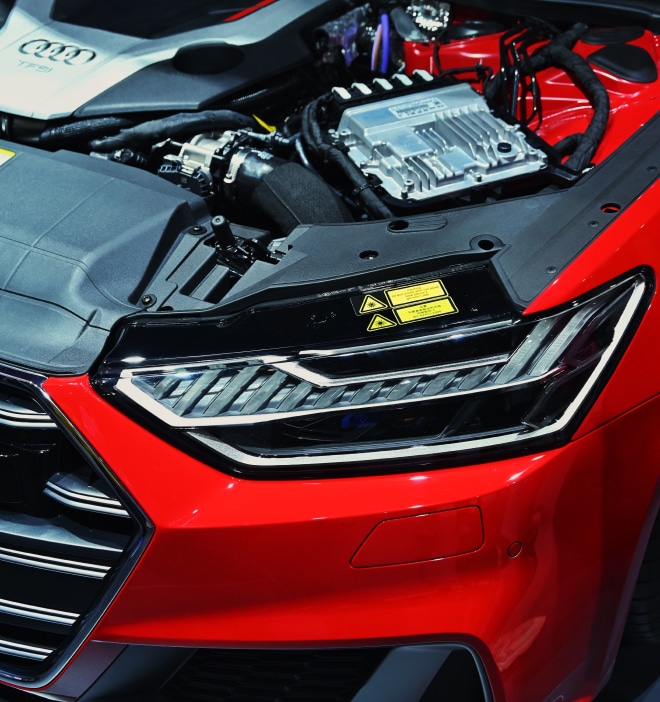
The performance of RVS Technology® is based on a triboceramic treatment that reduces fuel consumption and emissions. RVS Technology® is a real nanotechnological power treatment for engines, transmissions, and other mechanical devices. It is neither motor oil nor an oil additive, but a unique and innovative method of forming a new surface material.
The abbreviation RVS stands for Restores Vital Surfaces. As the name says, RVS Technology® protects your engine as it prevents and repairs many problems caused by normal wear, such as noise, smoke, excessive oil or fuel consumption, lack of power, or uneven compression. Corresponding benefits brought along by reduced friction can be obtained in many other mechanisms as well.
Test results Buy now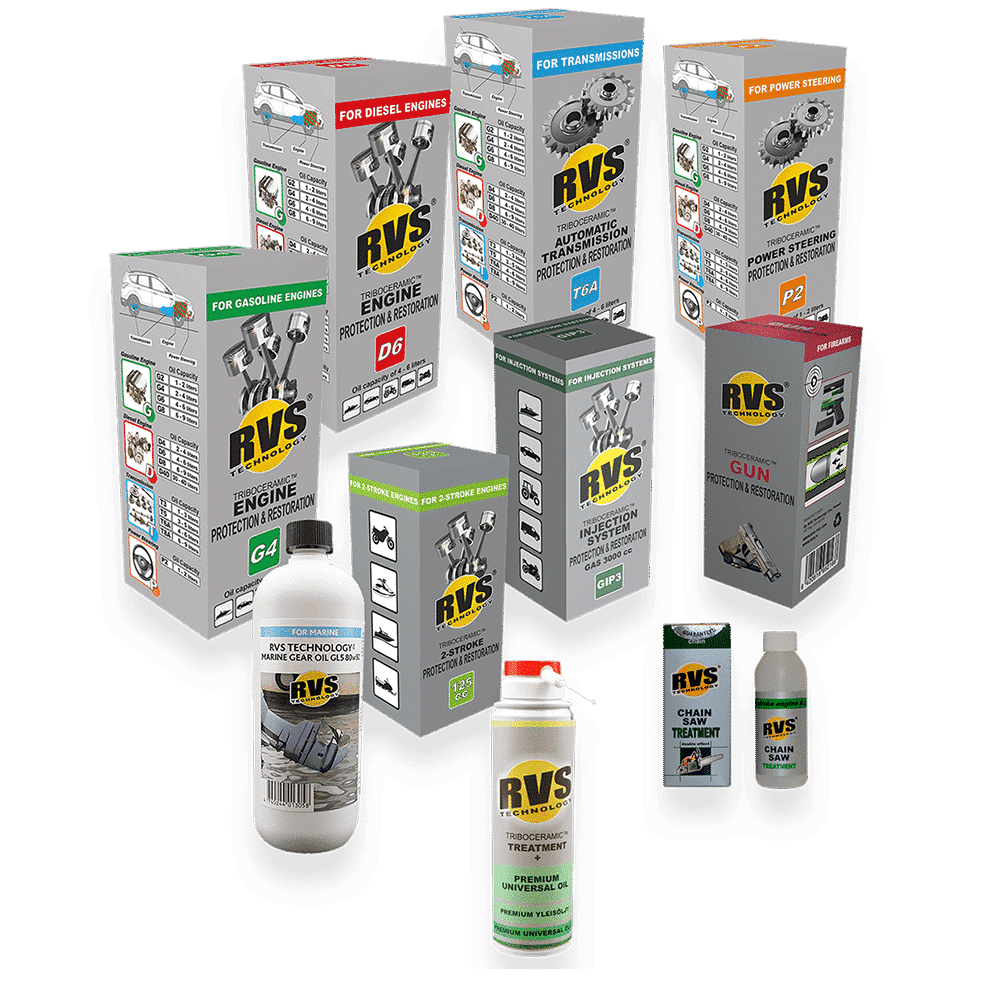
Finland-based, patented, and certified RVS Technology®
The performance of RVS Technology® is based on a triboceramic treatment that reduces fuel consumption and emissions. RVS Technology® is a real nanotechnological power treatment for engines, transmissions, and other mechanical devices. It is neither motor oil nor an oil additive, but a unique and innovative method of forming a new surface material.
The abbreviation RVS stands for Restores Vital Surfaces. As the name says, RVS Technology® protects your engine as it prevents and repairs many problems caused by normal wear, such as noise, smoke, excessive oil or fuel consumption, lack of power, or uneven compression. Corresponding benefits brought along by reduced friction can be obtained in many other mechanisms as well.
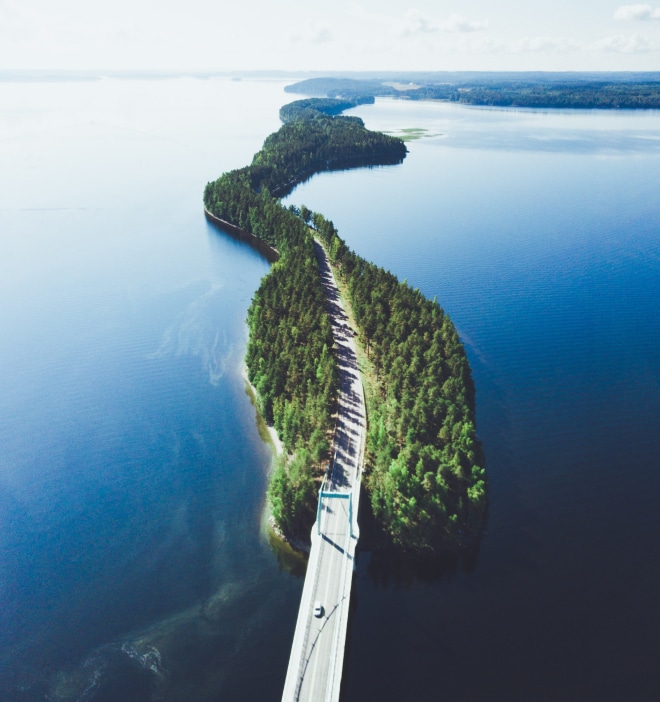
How does RVS Technology® work in practice?
RVS is the only technology that has the capability of restoring friction surfaces up to their original dimensions. The core of the technology lies in its ability to “identify” worn and defected zones as well as zones that are prone to wear. By using friction heat energy, certain parts of the RVS compound react and form a new surface structure autoreactively, i.e., automatically, without any external control. The process also ceases automatically when the ceramic surface has been formed and there is no more energy available. The process is thus safe, and the surface can never grow to an excess.
The thickness of the surface structure depends on the wear rate of the mechanism and the pressure that affects the surface during the operation of the mechanism. The more the surfaces have worn, the more there are internal shocks and, therefore, energy, i.e., heat, available for the restorative process.
Even with the most modern manufacturing methods, processing friction surface pairs to optimal dimensions is difficult and expensive. As in an RVS treatment, a new surface structure is formed automatically during normal operation; there is no need to dismantle the mechanism. This characteristic of RVS Technology® significantly intensifies the effects of a treatment, e.g., in industrial circumstances where restoring equipment has traditionally caused shut-downs of manufacturing processes.
By using RVS Technology®, restoring friction surface pairs occurs easily without expensive spare parts, logistics, handling expenses, or the need to contact a service department. As a result, you get a reliable mechanism for a long time.
Frequently asked questionsAn RVS treatment has a long-term effect
50%
longer lifetime
5–25%
fewer emissions
5–10%
lower consumption
3–15%
more power
See feedback from our customers
Customer feedbackYou can carry out an RVS treatment easily and quickly by yourself
You get the best possible result in an automobile engine with a mileage exceeding 40,000 km (25,000 miles) if you treat it twice. Using any separate engine flushing product is not necessary before either RVS treatment. We recommend that you carry out the first treatment 300–400 km (200–250 miles) before the oil change.
RVS Technology® is a result of research over several decades
The origin of the RVS technology goes back to extensive deep drilling operations. During drilling, it was discovered that at a certain depth, drill heads remained sharp for many times longer than they normally would.
During the subsequent research, it became clear that it was the mineral in the layers of rock that was causing this surprising effect. A group of researchers developed the idea of the effect of minerals further, and the first commercial RVS Technology® products were launched in 2001.
RVS story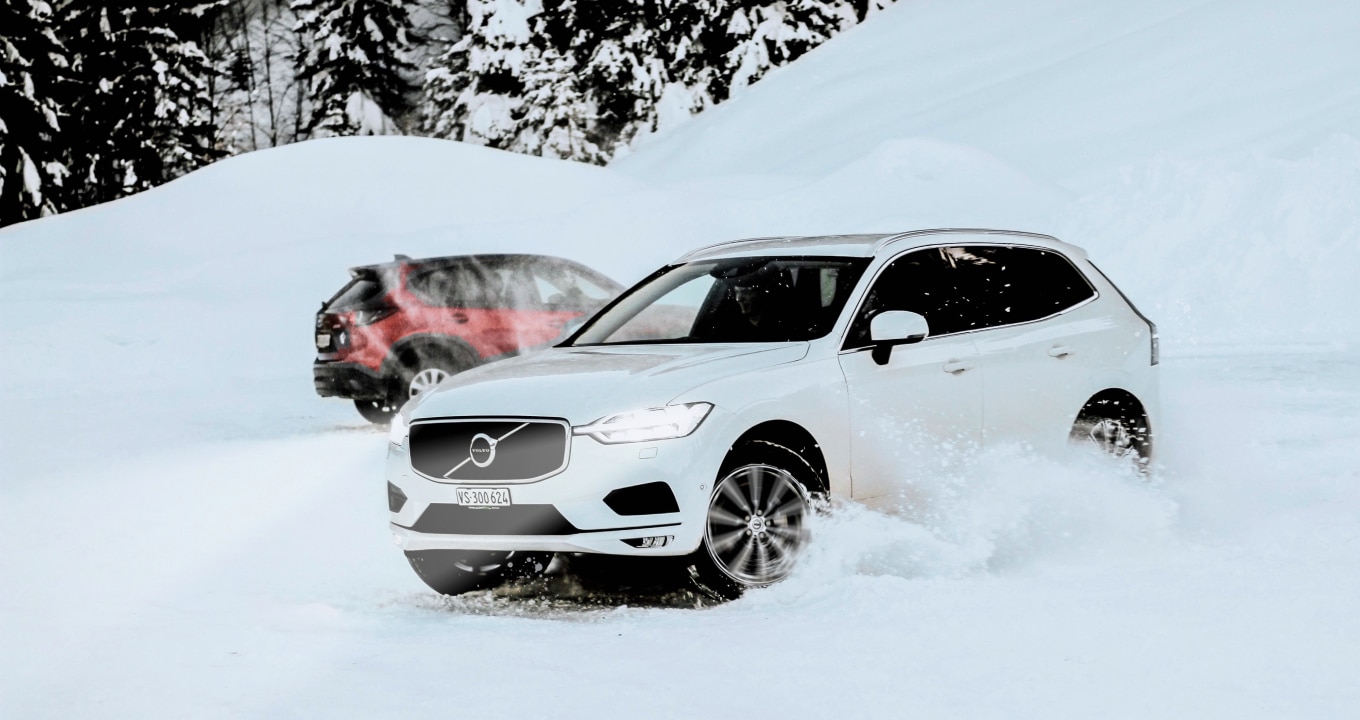
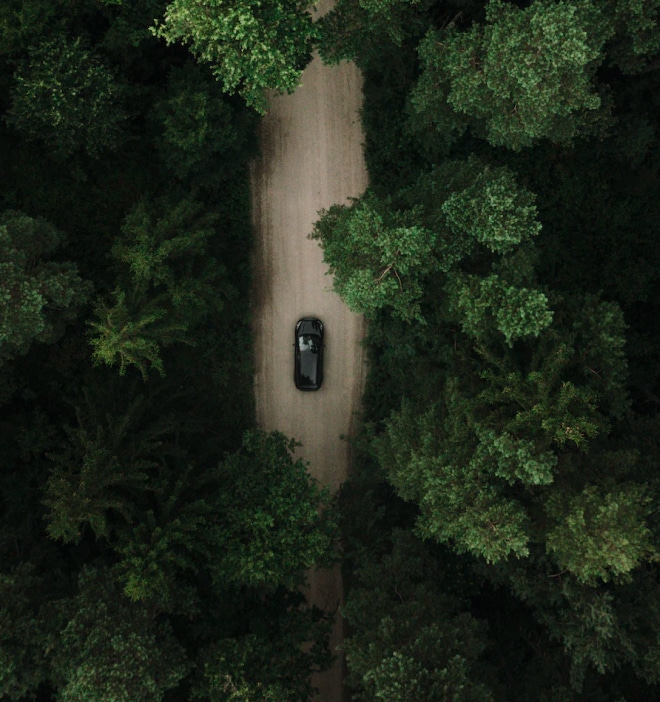
10 reasons to choose RVS Technology®
Contact us
If you wish to ask us about our products, you can contact us by using the form below.
"*" indicates required fields
